Metallurgy
Research
The research activity developed in the Metallurgy & Materials Research Unit is addressed to the synthesis, characterization and treatments of metallic materials. In particular the research topics are: Metallic Porous materials: in order to develop bioactive orthopedic and dental implants osteoblasts need to find proper paths to settle and grow. Porous materials possessing an interconnected structure and pores size in the range of 100 micorns represnt a proper choice. In addtion the presence of porosity reduce the stiffness of the implants making it closer to the bone mechanical properties. Starting form metallic powders of proepr size and composition open cell Ti-based foams are produced, so as Ti-based and AISI316L scaffolds. Different processing routes are used, such as gel-casting and direct ink writing (additive manufacturing). Foundry: Foundry is one of the most important metallurgical technologies based on solidification phenomena. The specific goal of this activity is the study of the complex interactions among the chemical-physical characteristics of the alloys, the process parameter, the micro-structural evolution, the mechanical and technological behaviour of the castings. Different kinds of alloys are investigated such as steels, cast irons, and aluminium, magnesium, copper and titanium alloys. Welding processes: Welding is a fundamental metallurgical process used to produce work-pieces in different fields of industry. The specific aim of this activity is to obtain an integrated vision of the welding process regarding different kinds of alloy such as stainless steels (duplex, super-duplex, super-austenitic stainless steels), super-alloys, titanium alloys, aluminium alloys. Both conventional and innovative welding process are taken into account (arc welding, laser, electron beam, friction stir welding) by means of analytical and numerical models (which predicts the thermal history, the microstructure and stress evolution during welding) so as experimental analyses (optical microscopy, mechanical tests, X-ray diffraction, residual stresses measurements) Bioceramic Coatings: bioceramic coatings are applied on metallic implants to enhance their bioactivity. The main limitation of the present technology is the poor adhesion to the substrate. Aim of this branch of research is the improvment of adhesion between the coating and the substrate. The research is directed towards the development of novel bioceramic composition, the use of low cost technologies and the metallic surface functionalization.
The research activity developed in the Metallurgy Unit of Padova University is addressed to the synthesis, characterization and treatments of metallic materials. In particular the research topics are: Innovative coatings for enhance the corrosion resistance and the wear resistance properties of light alloys (titanium, aluminum, magnesium) Production of metallic powders by atomization for sintering Production of metallic nanoparticles by sonoelectrochemical synthesis Production and characterization of amorphous materials for fuel cells Extractive metallurgy from ores and wastes materials.
The research activity developed in the Metallurgy Unit is addressed in particular to:
Foundry: Foundry is one of the most important metallurgical technologies based on solidification phenomena. The specific goal of this activity was the study of the complex interactions among the chemical-physical characteristics of the alloys, the process parameter, the micro-structural evolution, the mechanical and technological behaviour of the castings. Different kinds of alloys has been investigated such as steels, cast irons, and aluminium, magnesium, copper and titanium alloys. An integrated and interdisciplinary approach was developed, which was able to couple the experimental remarks with the results obtained by analytical and numerical models of the different physical phenomena involved (fluid dynamics, solidification, micro-structural evolution, thermal and residual stresses development). This kind of approach was useful, among other things, for the optimisation of the processes included those with a high content of innovation (semi-solid, squeeze casting).
Welding processes: Welding is a fundamental metallurgical process used to produce work-pieces in different fields of industry. The specific aim of this activity was to obtain an integrated vision of the welding process regarding different kinds of alloy such as stainless steels (duplex, super-duplex, super-austenitic stainless steels), super-alloys, titanium alloys, aluminium alloys. Both conventional and innovative welding process were taken into account (arc welding, laser, electron beam, friction stir welding). This goal was reached by means of the development of analytical and numerical models (which predicts the thermal history, the microstructure and stress evolution during welding) and experimental analyses (optical microscopy, mechanical tests, X-ray diffraction, residual stresses measurements)
Precious alloys: Precious alloys and the correspondent technological processes are a peculiarity of the territory of Vicenza which is characterized by a significant number of little firms. The specific aim of this activity was to give to the existing empiric approaches some scientific bases. In particular, problems regarding soldering processes were analysed (planning of a device and a procedure for the evaluation of the wettability index as a function of process parameters and chemical composition of the alloy). Lost wax Casting processes (analysis of defects and materials), innovative processes (Nd-YAG laser welding, powder metallurgy, induction annealing) were also studied.
Innovative materials: In most industrial applications there is a great demand of new materials able to satisfy the increasing performance requirements. The specific aim of this activity was to develop methodologies, procedures, criteria, significant examples for the industrial introduction of innovative materials. In detail, it has been worked on:
– titanium and its alloys: study (experimental and simulation) of casting processes for biomedical applications, characterisation of the surface of cast and/or wrought titanium alloys, set up of surface treatments for optimising osteo-integration;
– aluminium metal matrix composites: production of alloys reinforced with ceramic foams, optimisation of welding processes applied to metal matrix composites;
– nano-materials: achievement of a data-base about production processes, characteristics and kinds of application;
– alloys obtained by sintering: analysis of the optimal combination between matrix and diamond for tools, study of the behaviour during sintering of the precious alloys, mechanical alloying processes carried out on duplex andsuperduplex stainless steels.
Educational Program
Educational activity is carried out at the University of Padova by courses of Metallic Materials Technology, Corrosion, Steelmaking processes belonging to the Faculty of Engineering, within the frame of Materials Engineering Master Degree. Advanced courses pertaining to the area of metallic materials engineering and addressed to post graduates, doctoral students and professionals are offered.
The teaching activity of the Metallurgy Unit of Vicenza University is lead in various Courses of the Engineering Faculty, concerning Metallurgy and Metallic Materials, Metallurgical Plants, New metallurgical processes, Metallurgy of gold and precious alloys. They are also involved in a Course of the Medicine Faculty, concerning Biomaterials for Audio-prosthesis implants.
Since various years, inside the framework of the Centre of Mechanics of Biological Materials, they are giving metallurgy lessons about Titanium metallurgy and processes during courses about Implantology. The Metallurgy Unit has also carried out the scientific coordination of two Leonardo Pilot Projects:
- Coprofound, aimed at developing training tools about simulation of casting processes,
- Metro, aimed at setting up metallurgy courses by e-learning methodologies
Equipment
The Metallurgy Unit of Padova has laboratories for metallurgical characterization. The equipments in these labs are: Equipments for metallographic preparation, Optical microscopes interfaced with a digital analysis image system, Hardness and a microhardness testing devices, Scanning Electron Microscopy equipped with EDSX and WDS microprobes, Four axis X-ray diffractometer, X-ray Fluorescence Spectrometer, Glow discharge Optical Spectrometer, Transmission Electron Microscopy 120 Kev, Potentiostats for investigation of corrosion resistance of metallic materials Moreover, the Unit is equipped of an Atmospheric Plasma for surface treatments of different classes of materials and of a Sonoelectrochemical apparatus for production of metallic nanoparticles.
The Metallurgy Unit of Vicenza has set up two laboratories for metallurgical characterisation and has the availability of one laboratory for mechanical characterisation, one mechanical workshop and one computer laboratory. In such laboratories, there are equipment and know-how for investigating microstructure, defects and mechanical behaviour (both static and dynamic) of metallic materials: a complete set of equipment for metallographic preparation of specimens (cutting and micro-cutting machines, systems for cold and hot resin mounting of specimens, machines for grinding, polishing and lapping, devices for chemical and electro-chemical etching); two light and one stereographic microscopes, both interfaced with a system for acquiring, elaborating and analysing images; a hardness and a microhardness testing devices; a salt-spray machine for accelerated corrosion tests; a scanning electron microscopy, with an EDX microprobe; a X-ray diffractometer; an infrared camera, for the acquisition of thermal maps (working range: from -20°C to 1400°C, acquisition rate: up to 20 images/s); an industrial X-ray device for non-destructive radiographic testing; tensile and axial and multi-axial fatigue testing machines; numerical codes for simulation of metallurgical (casting, welding) processes.
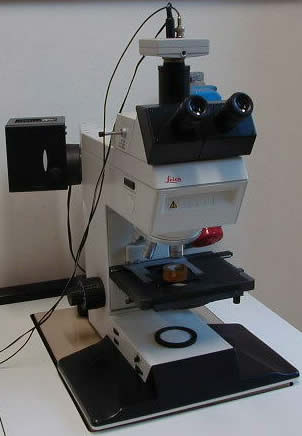
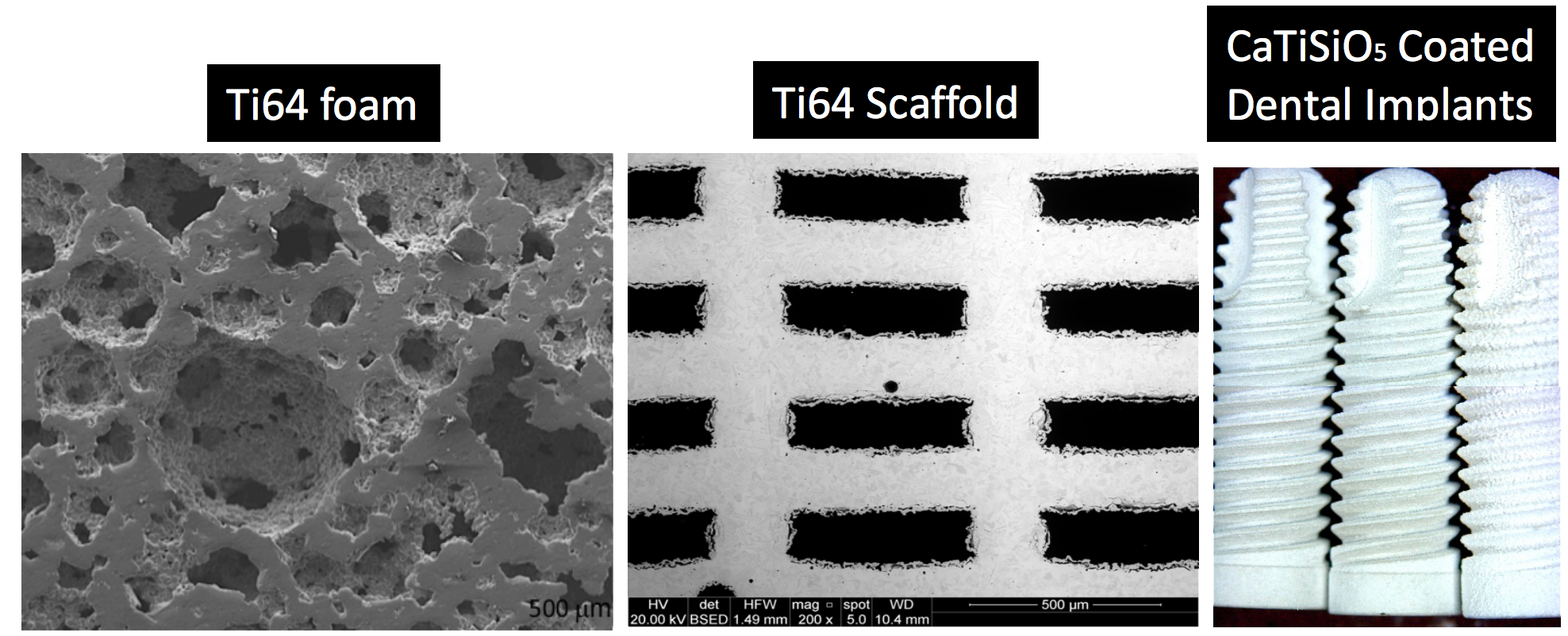
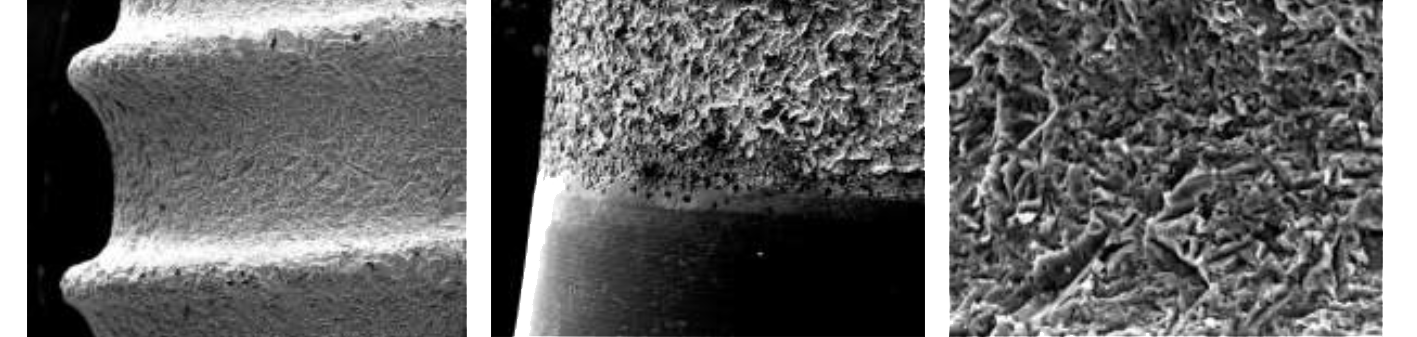