Science and Technology of Ceramics
Research Activity
The activity on Science and Technology of Ceramics is supported by the Advanced Ceramics & Glasses group, co-chaired by Prof. Paolo Colombo and Prof. Enrico Bernardo. The group focuses its activity mainly in the following topics:
- Nanostructured ceramic composites from preceramic polymers and fillers
- Advanced porous ceramic components
- Additive manufacturing (3D printing) of ceramics, including glasses
- Bioceramics from novel formulations and novel processing
- Monolithic and cellular glasses and glass-ceramics
- Novel construction materials from inorganic waste and/or recycled glasses [‘Up-cycling technologies’]
- Porous geopolymers (and alkali-activated materials)
The group possesses a wide expertise in the preparation of highly porous bioactive glass-ceramics, according to distinctive method, based on the processing of silicone polymers, combining synthesis and shaping. Glass-ceramics, in fact, may derive from the direct firing at 900-1100 °C of mixtures of silicone resins with CaO and MgO precursors, comprising also phosphates and borates as minor filler. The resulting phase assemblage, comprising silicate crystals immersed in a glassy phase, mimics that available from the sinter-crystallization of the glass with the same overall composition (Fig.1) The silicone-based mixtures, besides offering advantages in the synthesis, are particularly interesting for the application of additive manufacturing (AM) techniques, in turn aimed at the fabrication of highly porous 3D-scaffolds (Fig.2, left). As an example, direct ink writing of silicone/fillers mixtures leads to reticulated scaffolds with a remarkable compressive strength, ranging from 3.5 to 5.3 MPa, for a total porosity between 65 and 75%. Operating with sodium phosphate hydrate, glass-ceramic foams are easily achieved by water release, at 300-350 °C, from the dehydration of the same fillers, before ceramization upon firing at high temperatures. The foams are comparable results, in terms of strength and porosity, with reticulated scaffolds (Fig.2, right).
A second key to the development of highly porous glass-ceramics, to be used for bone tissue applications, consists of the sinter-crystallization process. According to selected chemical compositions, glass powders undergo viscous flow sintering, with concurrent crystallization, at 900-1000 °C. The remarkable increase of viscosity caused by the crystallization determines the ‘freezing’ of open-celled structures, previously obtained, from fine glass powders, using low temperature shaping technologies. These technologies comprise stereolithography of glass powders mixed with photocurable sacrificial binders (Fig.3, left) and frothing (intensive mechanical stirring, with the help of surfactants) of alkali activated aqueous suspensions of glass powders (suspensions undergoing progressive hardening by formation hydrated calcium silicate binding phase – Fig.3, right).
The research is supported by intensive international cooperation, e.g. with the University of Erlangen-Nuremberg (Prof. A.R. Boccaccini) and BAM Berlin (Prof. J. Guenster), also in the framework of European Projects, such as FunGlass (http://www.funglass.eu/funglass-project/) and AMITIE (http://www.rise-amitie.eu/).
Fig.1 – Application of the novel method to the obtainment of wollastonite-diopside glass-ceramics
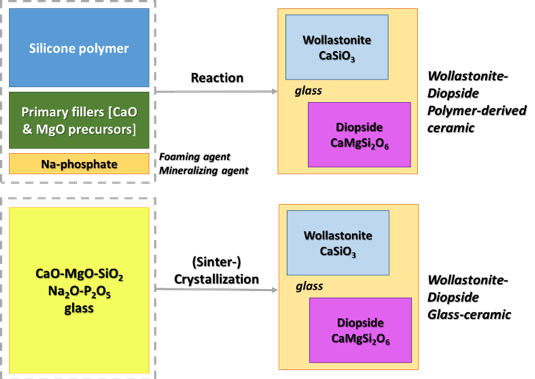
Educational Program
- Glass Science and Technology (master degree in Materials Engineering)
- Materials Selection and Design (master degree in Materials Engineering)
- Non-Metallic Materials and Materials Selection Criteria (master degree in Mechanical Engineering)
Fig.2 – Direct ink writing and foaming of silicone-based mixtures (from left to right: detail of direct ink writing in oil bath, overview of a 3D-printed scaffold, detail of open-celled glass-ceramic foam)
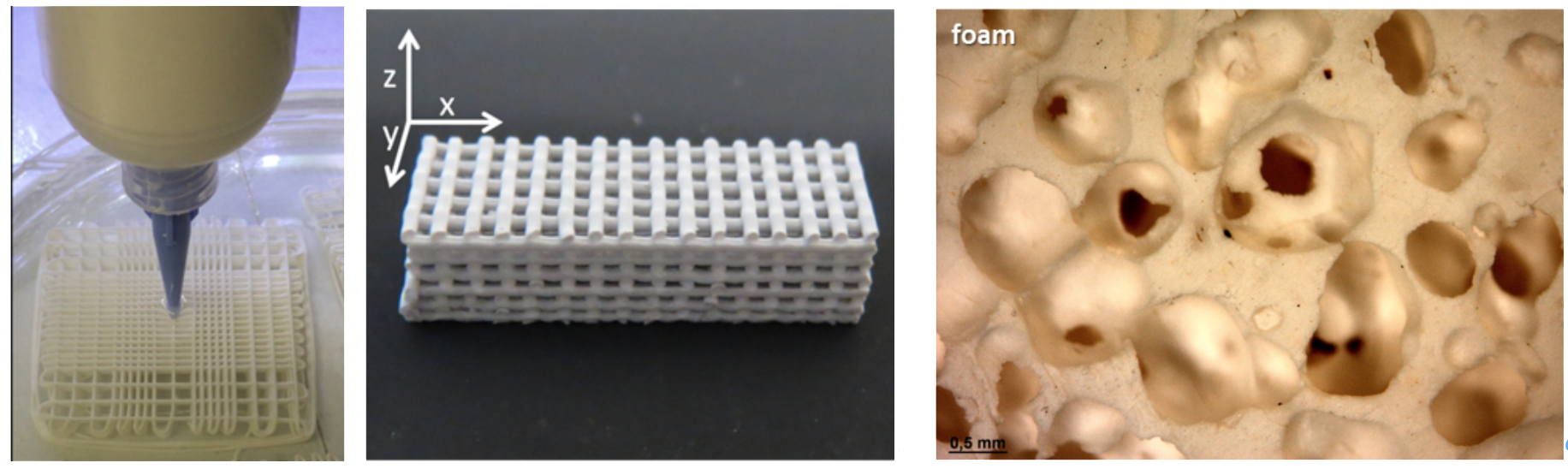
Equipment
The research on glasses, glass-ceramics and advanced ceramics is supported by state-of-the art instruments (e.g. high temperature muffle furnaces, DTA/TG, dilatometer, XRD, Vickers and Knoop micro-indenter, equipments for sample preparation and mechanical testing – mainly by bending or compression -, FTIR, ICP, SEM and EDX)
Fig.3 – Direct ink writing and foaming of silicone-based mixtures (from left to right: detail of direct ink writing in oil bath, overview of a 3D-printed scaffold, detail of open-celled glass-ceramic foam)
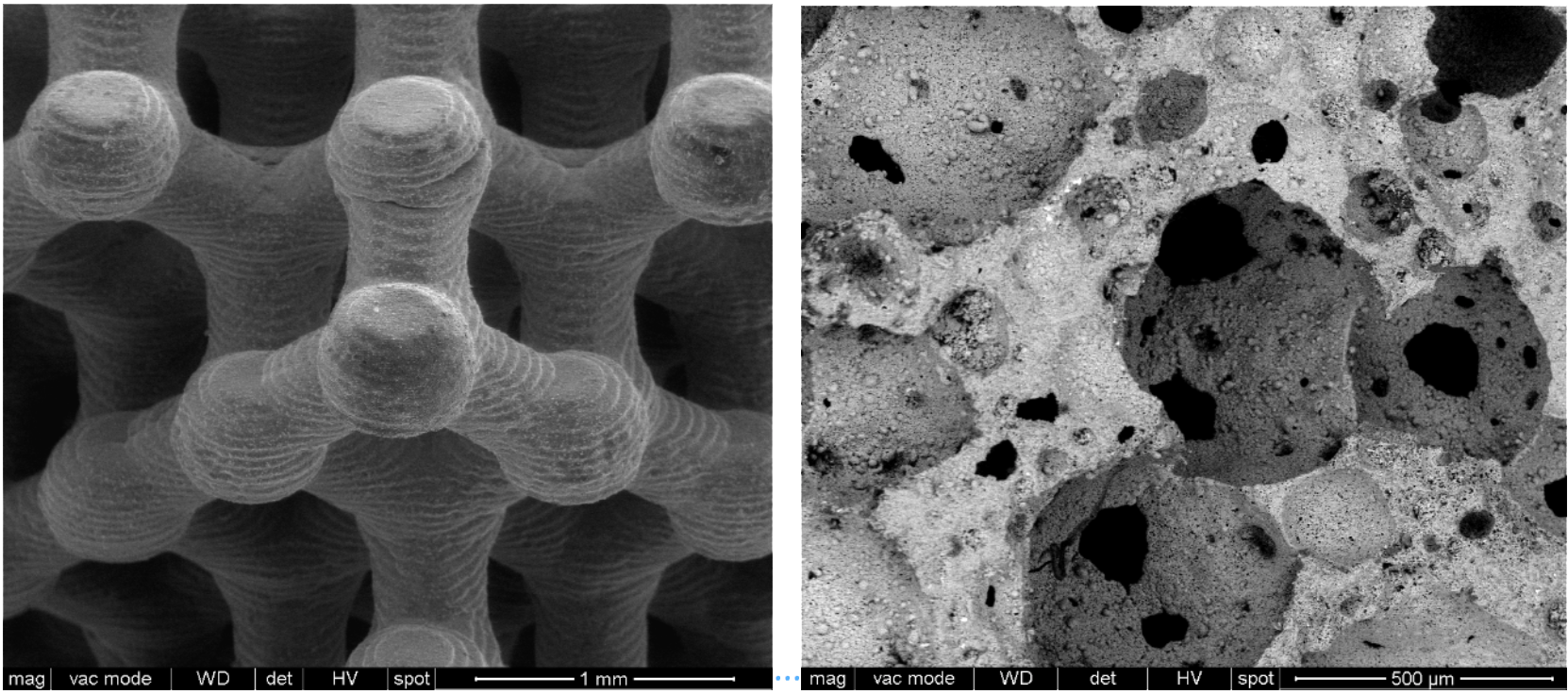